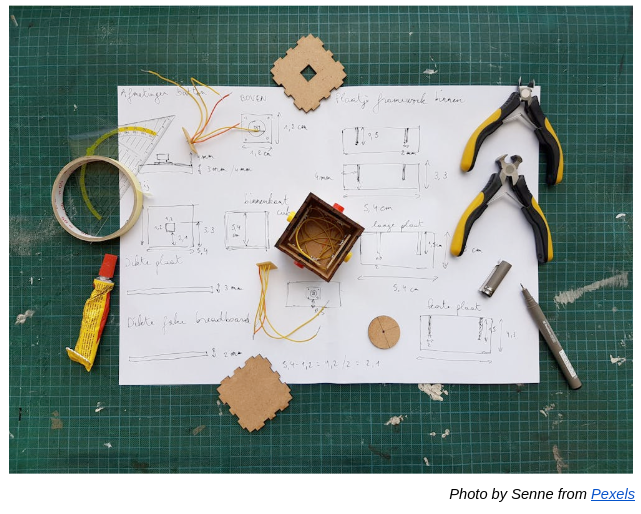
From Prototype to Product: 5 Tips to Design an Innovation for Manufacturing
There’s a big difference between a prototype and a product. To be considered successful, a prototype simply needs to work. A product, on the other hand, must make a profit, which means it must be optimized.
To turn a working prototype into a successful product, you cannot simply reproduce the prototype at scale. You must consciously design for manufacturing, to ensure a baseline of quality while minimizing costs.
This part of the innovation process is often given short shrift, but it is absolutely necessary. Your prototype may be a success, but without proper design, your product will fail. These 5 questions will help guide you through thoughtful product design.
#1: How Will You Package Your Solution?
On the surface, packaging your solution seems simple. Just go to any store, buy a container off the shelf, then stuff your solution inside, right? Wrong. This is actually one of the hardest aspects of manufacturing.
You’d think it would be easy, but boxes are a pain to get. Premade ones in various sizes, configurations, and materials exist, but they almost never exactly fit the modifications you need. You might find the right shape but not the right size, or you’ll find the right size but in the wrong material. It’s like trying to find a needle in a haystack.
Usually, you end up having to order customized containers from China. You must consider exactly what you need. The size, shape, and material of the container will often be dictated by the specifications of the project or the requirements of the solution. For example, perhaps the solution is part of a larger device, and you know it needs to fit into a 12 inch by 12 inch space. Or maybe you know your solution needs to be protected from electrical interference, requiring a certain material.
#2: How Will Everything Interconnect?
When people put together the different pieces of their solution, they often think, “Oh, we’ll just throw it together, and it’ll work.” No, that ain’t gonna work. You have to work hard to fit everything together in your solution, especially when you’re working with tight specifications.
Figuring out how everything interconnects is another deceptively simple task. It’s not like a game of Tetris, where you simply need to fit each piece into the housing. More factors than just size and shape are at play here.
For example, how will you route the circuits so the wires don’t rub or cause interference? Or if one piece gets hot while another needs to stay cold, how will you handle it? Maybe you’re using lead acid batteries, and you know what lead acid batteries give off when they’re charged? Hydrogen. How does hydrogen act in an environment where there are sparks or super high voltage?
The interconnections and the packaging are often related, so think about them simultaneously.
#3: How Will the Solution Be Assembled?
You must also consider how each piece and the connections will be assembled. This impacts both the solution’s user friendliness and its reliability.
First, how will you set up the solution so that putting it together and using it is easy? How will people know how to plug it together correctly? How will they know which side is down? Design the product in a way that its assembly and use are as intuitive and clear as possible.
Next, how will you ensure the solution is reliable after assembly? Every connection needs to be secured: either snapped and locked into place or glued. Otherwise, parts are liable to fall off or slip out of place, and then the solution won’t work.
Try to make the assembly as easy and straightforward as possible, because “easy” in manufacturing equals cost savings.
#4: How Will the Solution Handle Real-World Conditions?
While a prototype just needs to work, the product must work in real-world conditions. To design a prototype for manufacturing, you need to account for those real-world conditions.
Think about all the things the solution is going to be subjected to. Cold? Heat? Pressure? Moisture? Physical jostling? Shipping by the lowest-cost, least-predictable, ham-handed shipper (read USPS)?
Based on the real-world conditions, how will you manufacture your solution accordingly? Are you going to seal it? If it’s in a dusty environment, how do you exchange air without the solution getting full of dust? How waterproof does it need to be? Does it need to be moisture-proof or submersible? What about the weather?
Be sure to consider the safety—and the stupidity—of the user. Are there certain user behaviors you need to prevent? For example, putting a car into reverse while driving is terrible for the transmission, so many newer cars have features to prevent this. Or if you’re dealing with high-voltage, high-current electricity, you need to really pay attention to how you’re managing that, or someone will get knocked on their ass.
#5: What Will the Solution Look Like?
They say not to judge a book by its cover, but the reality is that looks matter. As the Fernando rule says: it’s better to look good than be good.
Imagine you’re trying to sell your product to a client or trying to secure funding from a VC. Do you want to show them a piece of junk that looks like it was glued together by a child with a bunch of wires hanging out? Or do you want to show them a polished, sleek product that makes it look like you know what you’re doing?
People might say they don’t care what a solution looks like, but that’s a lie. Everybody cares what it looks like. Even if only subconsciously, the look of a solution changes people’s perception of it. It doesn’t need to be gold and encrusted in diamonds, but it needs to be presentable.
The Power of Product Design
Most project plans wait until the last minute to think about design for manufacturing, and most people do not like to spend the required amount of money to ensure proper product design, to their own demise. A great project can be killed by waiting too late to focus on the mechanical aspects of the design.
On the flip side, with thoughtful consideration of your solution’s packaging, interconnections, assembly, real-world requirements, and aesthetics, you can turn your prototype into a product that delivers results.